Business Inventories: A Comprehensive Overview: 1 Define Business Inventories
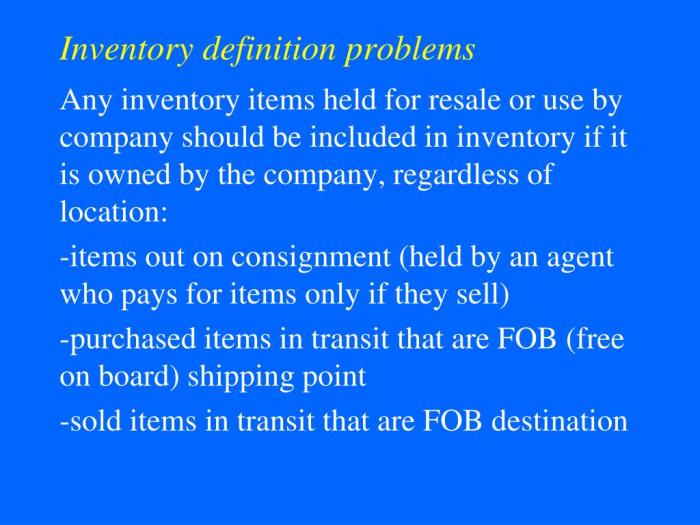
Source: slideserve.com
1 define business inventories – Business inventories represent a crucial aspect of a company’s operational efficiency and financial health. Understanding their composition, management, and valuation is essential for effective business strategy and profitability. This article delves into the intricacies of business inventories, exploring their definition, components, management techniques, valuation methods, associated costs and benefits, turnover, and inherent risks.
Definition of Business Inventories
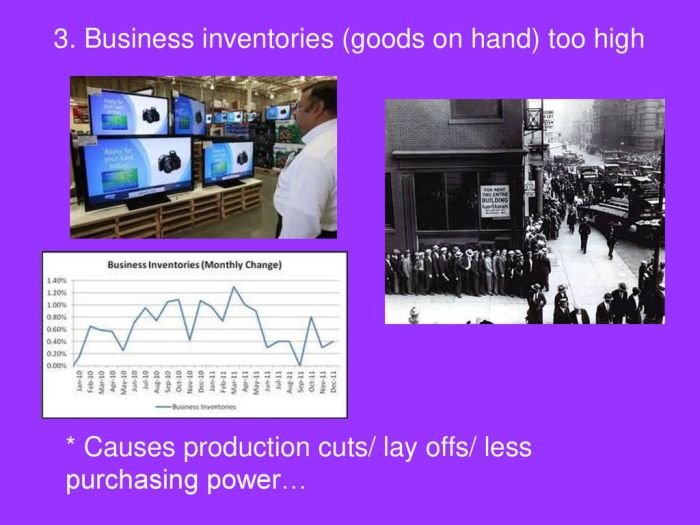
Source: slideplayer.com
Business inventories are the goods and materials held by a business for the purpose of eventual sale or use in production. These assets are a significant component of a company’s working capital and directly impact its profitability and cash flow. Accurate inventory management is crucial for maintaining optimal stock levels, minimizing waste, and maximizing return on investment.
Examples include:
- Raw Materials: These are the basic inputs used in the production process, such as wood for furniture manufacturing or cotton for textile production.
- Work-in-Progress (WIP): These are partially finished goods that are still undergoing the production process. For example, a partially assembled car on an automobile assembly line.
- Finished Goods: These are completed products ready for sale to customers, such as packaged food items or manufactured clothing.
Accurate inventory management is paramount for business success. It allows businesses to meet customer demand, minimize storage costs, prevent stockouts, and reduce waste from obsolescence. Inadequate inventory management can lead to lost sales, increased storage costs, and ultimately, decreased profitability.
Inventory Valuation Methods
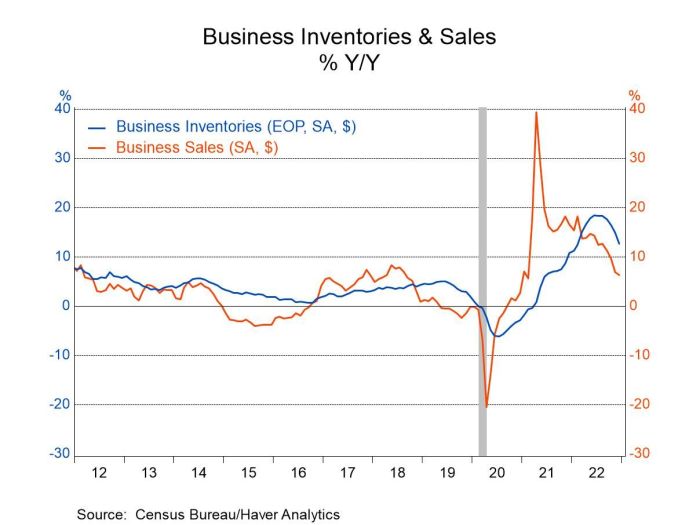
Source: amazonaws.com
Several methods exist for valuing inventory, each with its own implications for financial reporting. The three most common methods are First-In, First-Out (FIFO), Last-In, First-Out (LIFO), and Weighted-Average Cost.
Method | Description | Impact on Cost of Goods Sold (COGS) | Impact on Net Income |
---|---|---|---|
FIFO | Assumes the oldest inventory is sold first. | Lower during inflation, higher during deflation. | Higher during inflation, lower during deflation. |
LIFO | Assumes the newest inventory is sold first. | Higher during inflation, lower during deflation. | Lower during inflation, higher during deflation. |
Weighted-Average Cost | Calculates the average cost of all inventory items. | Reflects the average cost of goods sold. | Reflects the average net income. |
Components of Business Inventories
Business inventories typically comprise three main components: raw materials, work-in-progress (WIP), and finished goods. The proportion of each component varies significantly across industries, reflecting the nature of their production processes and sales cycles.
Raw materials form the foundation of the production process. WIP represents the ongoing transformation of raw materials into finished products, while finished goods are the final products ready for sale. Maintaining appropriate levels of each component is crucial for efficient operations and profitability. Excessive inventory ties up capital and increases storage costs, while insufficient inventory can lead to lost sales and dissatisfied customers.
Industries with varying inventory compositions include:
- Manufacturing: Typically characterized by high levels of raw materials and WIP, reflecting longer production cycles.
- Retail: Predominantly composed of finished goods, emphasizing quick turnover and responsiveness to consumer demand.
- Agriculture: May involve significant raw material inventories (e.g., harvested crops) subject to spoilage and seasonal fluctuations.
Inventory Management Techniques
Effective inventory management is critical for optimizing profitability and minimizing costs. Several techniques aim to achieve this goal, including Just-in-Time (JIT) and Economic Order Quantity (EOQ).
A simple inventory management system for a small retail business might include:
- Regular stocktaking to track inventory levels.
- Use of a point-of-sale (POS) system to monitor sales and automatically update inventory records.
- Setting reorder points for each item based on sales history and lead times.
- Regular review of inventory levels to identify slow-moving or obsolete items.
Implementing a Just-in-Time (JIT) system involves a step-by-step process:
- Analyze sales data to predict future demand.
- Establish strong relationships with suppliers to ensure timely delivery.
- Implement a system for tracking inventory levels in real-time.
- Develop a flexible production schedule to adapt to changes in demand.
- Continuously monitor and improve the system’s efficiency.
Inventory Valuation Methods: Detailed Examples
Let’s illustrate the three main inventory valuation methods with simple examples:
FIFO (First-In, First-Out)
Assume a company purchased 10 units at $10 each and later 15 units at $12 each. If they sell 12 units, FIFO assumes the 10 oldest units were sold first.
Units | Cost per Unit | Total Cost |
---|---|---|
10 | $10 | $100 |
2 | $12 | $24 |
Total | $124 |
Cost of Goods Sold (COGS) under FIFO: $124
LIFO (Last-In, First-Out)
Using the same scenario, LIFO assumes the 12 newest units were sold first.
Units | Cost per Unit | Total Cost |
---|---|---|
12 | $12 | $144 |
Cost of Goods Sold (COGS) under LIFO: $144
Weighted-Average Cost
The weighted-average cost is calculated by dividing the total cost of goods available for sale by the total number of units available for sale.
Units | Cost per Unit | Total Cost |
---|---|---|
10 | $10 | $100 |
15 | $12 | $180 |
Total | $280 |
Total Units: 25
Weighted-Average Cost: $280 / 25 = $11.20 per unit
COGS for 12 units: 12
– $11.20 = $134.40
Different valuation methods impact financial statements by altering the reported cost of goods sold and net income. These differences can affect tax liabilities and investor perceptions.
Inventory Costs and Benefits
Maintaining inventory involves both costs and benefits. Careful management is needed to balance these aspects for optimal profitability.
Costs | Benefits |
---|---|
Storage costs (rent, utilities, security) | Meeting customer demand |
Insurance costs | Avoiding stockouts and lost sales |
Obsolescence costs (spoilage, outdated items) | Taking advantage of bulk purchase discounts |
Handling and transportation costs | Smoother production processes |
Inventory taxes | Improved cash flow (in some cases) |
Efficient inventory management directly impacts a company’s cash flow. Excessive inventory ties up capital, reducing available funds for other business activities. Conversely, insufficient inventory can lead to lost sales and reduced cash inflow.
Inventory Turnover and its Significance, 1 define business inventories
Inventory turnover is a crucial metric reflecting how efficiently a company manages its inventory. It’s calculated as the cost of goods sold divided by the average inventory.
A high inventory turnover rate generally indicates efficient inventory management, while a low rate may suggest overstocking or slow sales. The optimal turnover rate varies significantly across industries, depending on factors like product perishability and demand patterns.
Example: A hypothetical scenario where a company improves its inventory turnover from 2 to 4 would mean that they are selling their inventory twice as fast, freeing up capital and potentially increasing profitability.
Inventory Risks and Mitigation Strategies
Several risks are associated with inventory management, including theft, damage, obsolescence, and spoilage. Effective mitigation strategies are crucial to minimizing these risks and protecting a company’s assets.
A robust inventory control system should incorporate:
- Security measures: Implementing physical security measures such as surveillance systems, access controls, and secure storage facilities to prevent theft and damage.
- Proper storage: Using appropriate storage facilities and methods to protect inventory from damage, spoilage, and obsolescence. This includes climate control for temperature-sensitive goods and organized storage for easy access and tracking.
- Effective forecasting: Utilizing accurate demand forecasting techniques to minimize overstocking and reduce the risk of obsolescence. This involves analyzing historical sales data, market trends, and seasonal variations.
- Regular stocktaking and audits: Conducting regular physical inventory counts and audits to verify inventory levels and identify discrepancies. This helps in detecting shrinkage, damage, or obsolescence.
- Technology integration: Implementing inventory management software and barcode/RFID systems to automate inventory tracking, improve accuracy, and provide real-time visibility into inventory levels.
- Insurance: Securing adequate insurance coverage to protect against losses due to theft, damage, or other unforeseen events.
- Employee training: Providing proper training to employees on inventory handling procedures, security protocols, and best practices to minimize errors and losses.
FAQs
What is the impact of inaccurate inventory data?
Inaccurate inventory data leads to poor decision-making, resulting in lost sales due to stockouts, excess holding costs due to overstocking, and inaccurate financial reporting.
How often should inventory be reviewed?
The frequency of inventory review depends on factors like inventory turnover rate and business type. Regular reviews, at least monthly, are generally recommended, with more frequent checks for fast-moving items.
What are some common inventory management software options?
Many software options exist, ranging from simple spreadsheet programs to sophisticated enterprise resource planning (ERP) systems. The best choice depends on business size and needs.
How does inventory management relate to customer satisfaction?
Effective inventory management directly impacts customer satisfaction. Meeting customer demand through readily available stock enhances their experience and fosters loyalty, while stockouts can lead to dissatisfaction and lost sales.