Raw Materials Inventory
3 inventory accounts for a manufacturing business – Accurate tracking of raw materials is paramount for efficient manufacturing. Without precise inventory data, production delays, increased costs, and inaccurate financial reporting become significant risks. Effective raw materials management ensures the right materials are available at the right time, minimizing waste and maximizing profitability.
Raw Materials Inventory Tracking Methods
Several methods exist for tracking raw materials, each with its own implications for cost of goods sold and inventory valuation. The choice of method depends on factors such as the nature of the raw materials, the inventory turnover rate, and the company’s accounting policies.
- First-In, First-Out (FIFO): This method assumes that the oldest raw materials are used first. It generally results in a more accurate reflection of current costs on the balance sheet.
- Last-In, First-Out (LIFO): This method assumes that the newest raw materials are used first. It can lead to lower taxable income during periods of inflation, but may not accurately reflect current inventory values.
- Weighted-Average Cost: This method calculates the average cost of all raw materials on hand. It simplifies inventory valuation but may not reflect the true cost of goods sold as accurately as FIFO or LIFO.
Raw Materials Inventory Management System
A robust system encompasses receiving, storage, and issuing procedures. Clear documentation and regular audits are crucial.
- Receiving: Upon arrival, raw materials should be inspected for quality and quantity, then recorded in the inventory system. Discrepancies should be immediately addressed.
- Storage: Materials should be stored in a designated area, organized for easy access and identification. Proper storage conditions (temperature, humidity, etc.) must be maintained to prevent spoilage or degradation.
- Issuing: A formal requisition process should be in place to track material usage. This process should be integrated with the production planning system to ensure accurate material allocation.
Sample Raw Materials Inventory Report
This table illustrates a basic inventory report. In a real-world scenario, this would be dynamically generated from the inventory management system.
Item | Quantity | Unit Cost | Total Value |
---|---|---|---|
Steel Bars | 100 | $50 | $5000 |
Aluminum Sheets | 50 | $25 | $1250 |
Plastic Components | 2000 | $1 | $2000 |
Work-in-Progress (WIP) Inventory
Accurately valuing WIP inventory presents challenges due to its incomplete nature. The valuation methods used directly impact the financial statements and profitability calculations.
Challenges in Valuing WIP Inventory
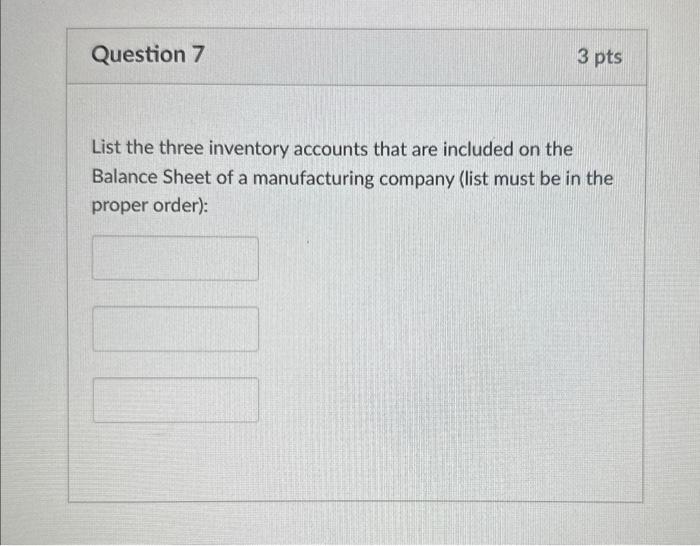
Source: cheggcdn.com
The inherent difficulty lies in assigning costs to partially completed goods. These costs include direct materials, direct labor, and manufacturing overhead. Accurate tracking of these costs throughout the production process is essential.
Tracking Material Movement Through Production
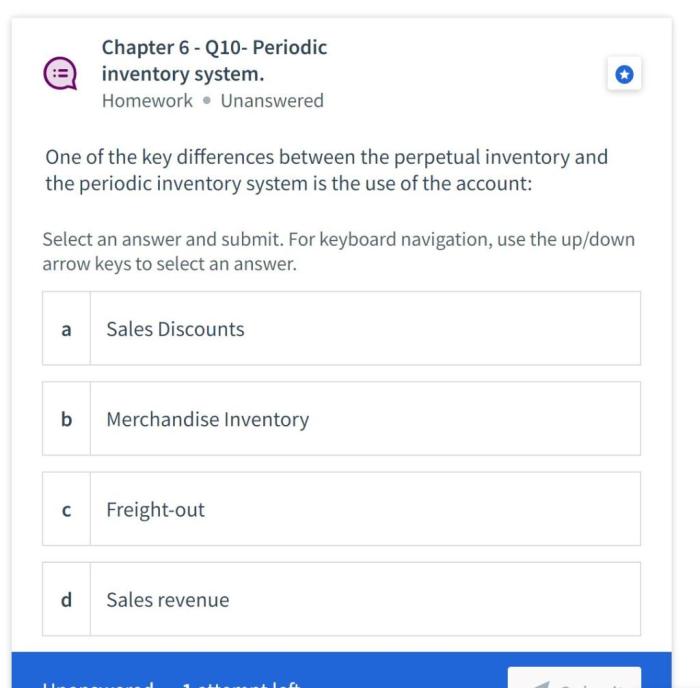
Source: cheggcdn.com
Effective tracking requires a system that monitors the movement of materials at each stage of production. This often involves barcoding, RFID tagging, or other technologies to provide real-time visibility into the production process.
Allocating Overhead Costs to WIP
Overhead costs, such as rent, utilities, and depreciation, must be allocated to WIP inventory. Common methods include machine hours, direct labor hours, or a predetermined overhead rate.
Costing Methods for WIP Inventory
Different costing methods provide varying levels of accuracy and complexity. The choice depends on the manufacturing environment and the level of detail required.
- Job Order Costing: This method tracks costs for each individual job or batch. It is suitable for custom or small-batch production.
- Process Costing: This method averages costs across a large volume of similar products. It is more efficient for mass production.
- Job Order Costing:
- Advantages: Accurate cost tracking for individual jobs, suitable for customized products.
- Disadvantages: More complex and time-consuming, less efficient for mass production.
- Process Costing:
- Advantages: Simpler and more efficient for mass production, lower administrative costs.
- Disadvantages: Less accurate cost tracking for individual units, not suitable for customized products.
Finished Goods Inventory
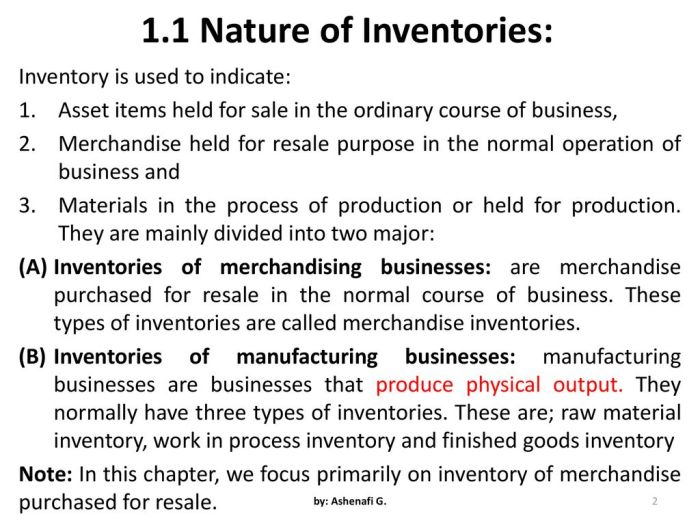
Source: slideplayer.com
Maintaining the optimal level of finished goods inventory is a balancing act between meeting customer demand and minimizing storage costs and the risk of obsolescence.
Factors Influencing Optimal Finished Goods Inventory
Several factors influence the ideal level, including sales forecasts, lead times for production, storage capacity, and the cost of holding inventory. Accurate forecasting and efficient production planning are key to optimization.
Risks of Excessive Finished Goods Inventory
Holding excessive inventory exposes businesses to various risks, including obsolescence, spoilage, damage, theft, and increased storage costs. These costs can significantly impact profitability.
Inventory Management Techniques for Finished Goods
Several techniques aim to optimize finished goods inventory levels and minimize associated risks.
- Just-in-Time (JIT): This method aims to minimize inventory by producing goods only when needed. It requires close coordination with suppliers and efficient production processes.
- Economic Order Quantity (EOQ): This model calculates the optimal order quantity to minimize total inventory costs (ordering and holding costs). It balances the costs of ordering frequently versus holding large quantities.
Calculating Finished Goods Inventory Value
Different costing methods yield different valuations. The choice of method influences the cost of goods sold and the gross profit reported on the income statement.
Costing Method | Calculation | Example (100 units @ $10 each) |
---|---|---|
FIFO | Cost of the oldest units | $1000 |
LIFO | Cost of the newest units | $1000 (assuming consistent cost) |
Weighted-Average | Average cost of all units | $1000 (assuming consistent cost) |
Inventory Valuation Methods
The choice of inventory valuation method significantly impacts the reported cost of goods sold and net income, and consequently, the tax liability. Understanding the nuances of each method is crucial for accurate financial reporting.
Impact on Financial Statements
FIFO generally results in higher net income during periods of inflation, while LIFO results in lower net income. Weighted-average provides a middle ground, smoothing out fluctuations in costs.
Situations Where Each Method is Most Appropriate
The suitability of each method depends on the specific circumstances of the business. FIFO is often preferred when inventory is perishable or quickly becomes obsolete. LIFO can be advantageous in inflationary environments for tax purposes. Weighted-average offers simplicity and is suitable for businesses with homogenous inventory.
Tax Implications
Tax laws often influence the choice of inventory valuation method. LIFO can reduce taxable income during inflation, but it’s not permitted under IFRS. Consult with a tax professional to determine the most tax-efficient method.
Comparative Analysis of FIFO, LIFO, and Weighted-Average
- FIFO:
- Advantages: Reflects current market values, generally leads to higher net income during inflation.
- Disadvantages: Can lead to higher taxes during inflation.
- LIFO:
- Advantages: Can reduce taxes during inflation, matches current costs with current revenues (to some extent).
- Disadvantages: May not accurately reflect current inventory values, not permitted under IFRS.
- Weighted-Average:
- Advantages: Simple to calculate, smooths out cost fluctuations.
- Disadvantages: May not accurately reflect the true cost of goods sold.
Inventory Management Strategies
Effective inventory management requires a system that integrates with production planning, minimizes costs, and utilizes technology to enhance efficiency and accuracy.
Integrating Inventory Management with Production Planning
A well-integrated system uses sales forecasts and production schedules to determine the required raw materials and finished goods inventory levels. This ensures that production is not hampered by material shortages and that finished goods are available to meet customer demand.
Minimizing Inventory Holding Costs, 3 inventory accounts for a manufacturing business
Strategies include optimizing order quantities, improving forecasting accuracy, implementing efficient storage and handling procedures, and reducing lead times.
Use of Technology in Inventory Management
Technology significantly enhances inventory management. Barcode scanning and RFID tracking provide real-time visibility into inventory levels and movement. Inventory management software automates many tasks, reducing manual effort and errors.
Understanding the three core inventory accounts – raw materials, work-in-progress, and finished goods – is crucial for any manufacturing business. Efficient management of these accounts directly impacts profitability, and a robust system is essential. For a deeper dive into the practical application of inventory accounting, check out this helpful resource on +business +inventory +accounting +application. Proper accounting for these three inventory accounts ensures accurate financial reporting and effective decision-making.
Safety Stock Policy
A safety stock policy helps mitigate the risk of stockouts. The appropriate safety stock level depends on factors such as lead time variability, demand variability, and the desired service level.
A common approach to safety stock calculation involves using a formula that considers the average daily demand, lead time, and a safety factor based on the desired service level. For example:
Safety Stock = (Average Daily Demand x Lead Time) x Safety Factor
Let’s say the average daily demand is 10 units, the lead time is 5 days, and the desired service level corresponds to a safety factor of 2 (covering potential fluctuations in demand and lead time). The safety stock calculation would be:
Safety Stock = (10 units/day x 5 days) x 2 = 100 units
This means 100 units should be held as safety stock to ensure a high probability of meeting demand during lead time.
Key Questions Answered: 3 Inventory Accounts For A Manufacturing Business
What are the potential consequences of inaccurate inventory tracking?
Inaccurate inventory tracking can lead to production delays, stockouts, overstocking, inflated costs, inaccurate financial reporting, and ultimately, reduced profitability.
How often should inventory be physically counted?
The frequency of physical inventory counts depends on factors such as inventory turnover rate, the value of inventory, and the risk of loss or damage. Many businesses conduct cycle counts regularly, supplementing them with full physical inventories periodically.
What is the role of technology in modern inventory management?
Technology plays a crucial role, enabling real-time tracking, automated data collection (barcode scanning, RFID), improved forecasting, and optimized inventory levels. Software solutions integrate various aspects of inventory management, streamlining processes and reducing manual errors.