Inventory Management Methods for Based Businesses
Accounting for inventory based business – Inventory management is crucial for businesses that deal with physical goods. Effective inventory management ensures sufficient stock to meet customer demand while minimizing storage costs and preventing obsolescence. Choosing the right inventory valuation method significantly impacts financial reporting. This section explores different inventory management methods and their implications.
Comparison of FIFO, LIFO, and Weighted-Average Cost Methods, Accounting for inventory based business
The First-In, First-Out (FIFO), Last-In, First-Out (LIFO), and weighted-average cost methods are common approaches to inventory valuation. Each method affects the cost of goods sold (COGS) and net income differently, especially during periods of inflation and deflation.
Method | Cost of Goods Sold (Inflation) | Net Income (Inflation) | Cost of Goods Sold (Deflation) | Net Income (Deflation) |
---|---|---|---|---|
FIFO | Lower | Higher | Higher | Lower |
LIFO | Higher | Lower | Lower | Higher |
Weighted-Average | Between FIFO and LIFO | Between FIFO and LIFO | Between FIFO and LIFO | Between FIFO and LIFO |
For example, during inflation, FIFO reports lower COGS because older, cheaper inventory is sold first, resulting in higher net income. Conversely, LIFO reports higher COGS, leading to lower net income. During deflation, the effects are reversed.
Spreadsheet-Based Inventory Tracking System for Small Businesses
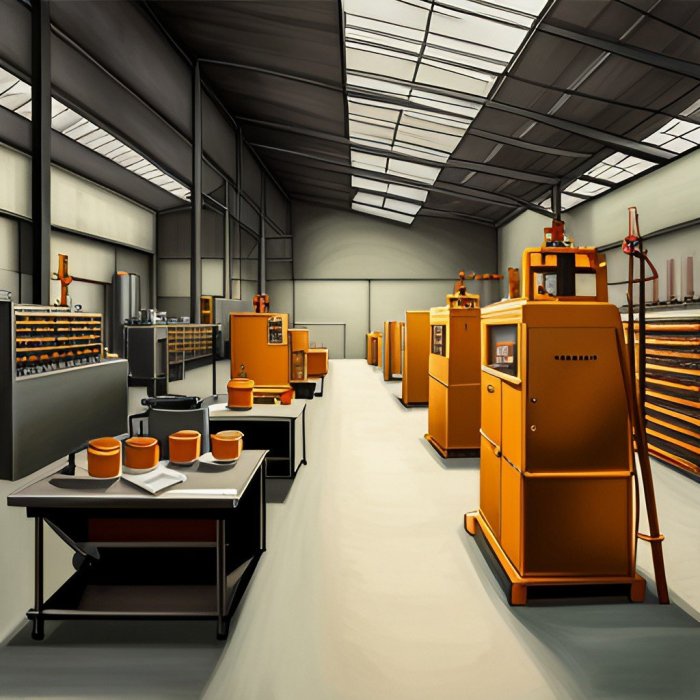
Source: accountingprofessor.org
A simple spreadsheet can effectively track inventory for small businesses. Columns can include product ID, product name, quantity on hand, unit cost, total value, reorder point, and supplier information. Formulas can calculate total value (quantityunit cost) and trigger alerts when stock reaches the reorder point. The spreadsheet should also allow for easy recording of inventory receipts and sales.
For instance, a simple SUM function can calculate total inventory value, while an IF function can flag items needing reordering. VLOOKUP can be used to automatically populate supplier information based on product ID.
Accurate accounting for inventory-based businesses is crucial for profitability. A key aspect is effectively managing your stock levels, which directly impacts your bottom line. For helpful guidance on this, check out this article on 4 keys to managing your new business’s inventory , which offers practical strategies. By implementing these strategies, you’ll improve your inventory control and subsequently enhance the accuracy of your financial reporting.
Importance of Regular Inventory Counts and Cycle Counting
Regular inventory counts, including cycle counting, are essential for maintaining accurate inventory records. Physical counts help identify discrepancies between recorded and actual inventory levels. Cycle counting involves counting a small portion of inventory regularly, reducing the time and disruption of a full physical count.
Procedures for a physical inventory count include assigning teams, establishing clear counting procedures, using standardized forms, and reconciling counts with inventory records. Discrepancies should be investigated and corrected.
Impact of Inventory on Financial Statements
Inventory valuation directly affects both the balance sheet and the income statement. The chosen costing method influences the reported value of inventory (balance sheet) and the cost of goods sold (income statement), impacting profitability.
Inventory Valuation’s Effect on Financial Statements
The balance sheet reflects inventory at its historical cost or net realizable value (NRV), whichever is lower. The income statement shows the cost of goods sold, calculated using the chosen inventory costing method (FIFO, LIFO, weighted-average). For example, using LIFO during inflation will result in a higher COGS and lower net income compared to FIFO.
Consider a scenario where a company has 100 units of a product. Using FIFO during inflation, the COGS will be lower than if LIFO were used, thus impacting net income.
Inventory Turnover Ratio and Days Sales in Inventory
The inventory turnover ratio measures how efficiently a company sells its inventory. It’s calculated as Cost of Goods Sold / Average Inventory. Days sales in inventory (DSI) indicates the number of days it takes to sell the average inventory. It’s calculated as 365 / Inventory Turnover Ratio. High turnover suggests efficient inventory management, while low turnover might indicate overstocking or slow sales.
Impact of Inventory Obsolescence and Write-Downs
Inventory obsolescence and write-downs significantly impact financial statements.
- Obsolescence: Outdated or damaged inventory reduces the value of assets on the balance sheet and increases COGS, lowering net income.
- Write-downs: When inventory’s market value falls below its historical cost, a write-down reduces the inventory value on the balance sheet and increases expenses on the income statement, impacting net income.
Inventory Control and Cost Reduction Strategies
Effective inventory control minimizes holding costs and ensures optimal stock levels. Techniques like Just-in-Time (JIT) and Economic Order Quantity (EOQ) help achieve this.
Comparison of JIT and EOQ Inventory Control Techniques
Technique | Advantages | Disadvantages | Suitability |
---|---|---|---|
Just-in-Time (JIT) | Reduced storage costs, minimized waste, improved efficiency | Requires precise demand forecasting, susceptible to supply chain disruptions | Suitable for businesses with stable demand and reliable suppliers |
Economic Order Quantity (EOQ) | Balances ordering and holding costs, minimizes total inventory costs | Assumes constant demand and lead times, doesn’t account for price discounts | Suitable for businesses with relatively stable demand and known ordering costs |
Minimizing Inventory Holding Costs
Holding costs include warehousing, insurance, taxes, and obsolescence. Strategies to minimize these costs include optimizing warehouse space, negotiating favorable insurance rates, implementing effective inventory control to reduce obsolescence, and exploring alternative storage solutions like cloud warehousing.
For example, negotiating bulk discounts from suppliers can reduce unit costs and improve profit margins, while implementing a robust inventory management system can reduce obsolescence by identifying slow-moving items.
Implementing an Inventory Management System with Barcode Scanning and RFID Technology
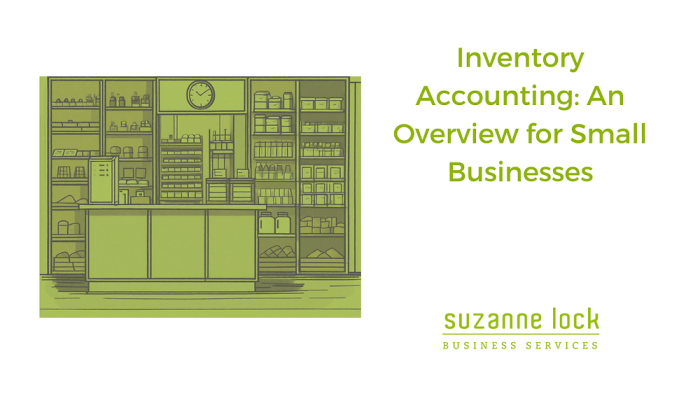
Source: wixstatic.com
Implementing a system incorporating barcode scanning and RFID technology offers several benefits, including improved accuracy, faster inventory counts, and real-time tracking. However, it requires initial investment in hardware and software, and staff training. The benefits outweigh the challenges for many businesses, leading to enhanced efficiency and reduced errors.
Inventory Accounting Software and Technology
Various software packages streamline inventory management. Choosing the right software depends on business size and specific needs.
Comparison of Inventory Management Software Packages
- Software A: Features real-time tracking, barcode scanning integration, and robust reporting capabilities. Suitable for medium to large businesses.
- Software B: Offers basic inventory tracking, suitable for small businesses with simple inventory needs. Lacks advanced features.
- Software C: Integrates with accounting software, providing a seamless workflow. Strong reporting features.
Role of Technology in Automating Inventory Processes
Technology automates various inventory processes, such as automated ordering systems triggered by low stock alerts, automated receiving systems using barcode scanners, and real-time inventory tracking using RFID tags. This reduces manual work, improves accuracy, and enhances efficiency.
Integration of Inventory Management Systems with Other Accounting Software
Integrating inventory management systems with accounting software (ERP systems) provides a centralized view of financial data, improving accuracy and efficiency. This integration automates data flow between inventory and accounting modules, reducing errors and saving time.
Legal and Regulatory Compliance for Inventory
Maintaining accurate inventory records and adhering to legal and tax regulations is crucial.
Importance of Proper Documentation and Record-Keeping
Proper documentation is vital for accurate inventory valuation, tax reporting, and preventing fraud. Documentation should include purchase orders, receiving reports, sales invoices, and inventory count records.
Tax Implications of Different Inventory Costing Methods
Different inventory costing methods have tax implications. The choice of method affects the reported COGS and therefore taxable income. Regulations may restrict the use of certain methods depending on the industry and business size.
Potential Legal Issues Related to Inventory Management
Inventory-related legal issues include fraud (e.g., theft, misrepresentation of inventory levels), and non-compliance with tax regulations. Implementing strong internal controls, regular audits, and employee training can help prevent and detect such issues.
Clarifying Questions: Accounting For Inventory Based Business
What are the potential penalties for inaccurate inventory accounting?
Penalties for inaccurate inventory accounting can range from financial penalties and interest charges due to incorrect tax filings to legal repercussions if fraudulent activity is involved. The severity depends on the nature and extent of the inaccuracy and applicable regulations.
How does inventory affect cash flow?
Inventory ties up significant capital. High inventory levels reduce cash flow as money is invested in unsold goods. Conversely, insufficient inventory can lead to lost sales and reduced cash flow. Effective inventory management is crucial for maintaining healthy cash flow.
How often should a physical inventory count be conducted?
The frequency of physical inventory counts depends on factors like inventory turnover rate, industry standards, and internal control requirements. Some businesses conduct them annually, while others opt for more frequent cycle counts.