Understanding Inventory Needs for Small Businesses
Automate inventory control small business – Efficient inventory management is crucial for small businesses to thrive. Poor inventory control can lead to lost sales, increased storage costs, and ultimately, reduced profitability. Understanding your inventory needs and implementing effective management strategies is key to success.
Common Inventory Challenges for Small Businesses
Small businesses often face unique inventory challenges. These include inaccurate inventory counts due to manual tracking, difficulty forecasting demand, inefficient ordering processes leading to stockouts or overstocking, and a lack of real-time visibility into inventory levels.
Key Inventory Metrics for Small Businesses
Tracking key metrics provides valuable insights into inventory performance. Essential metrics include inventory turnover rate (how quickly inventory is sold), carrying costs (costs associated with holding inventory), stockout rate (percentage of times an item is out of stock), and gross profit margin (profitability of sales).
Benefits of Automating Inventory Control
Automating inventory control offers numerous advantages for small businesses. Automation improves accuracy, reduces manual errors, streamlines processes, enhances efficiency, provides real-time data visibility, improves forecasting accuracy, and ultimately boosts profitability.
Manual vs. Automated Inventory Management
Feature | Manual System | Automated System |
---|---|---|
Accuracy | Prone to human error | Highly accurate, real-time data |
Efficiency | Time-consuming, labor-intensive | Streamlined processes, saves time and resources |
Cost | Low initial cost, high operational cost | Higher initial cost, lower long-term operational cost |
Scalability | Difficult to scale with business growth | Easily scalable to accommodate business expansion |
Choosing the Right Automation Tools
Selecting the right inventory management software is crucial for effective automation. Consider factors like business size, budget, specific needs, and integration capabilities with existing systems.
Comparing Inventory Management Software Options
Various software options exist, ranging from simple spreadsheet-based solutions to sophisticated cloud-based systems. Factors to compare include features, pricing, user-friendliness, scalability, and customer support. Examples include Zoho Inventory, QuickBooks Online, and Fishbowl Inventory.
Prioritizing Features in Inventory Management Software
When selecting software, prioritize features like real-time inventory tracking, automated ordering, reporting and analytics dashboards, integration with POS and accounting systems, barcode/RFID scanning capabilities, and mobile accessibility.
Integration Capabilities of Automation Tools
Seamless integration with existing systems like point-of-sale (POS) and accounting software is essential. This ensures data consistency and avoids manual data entry, reducing errors and saving time. Look for software with APIs or pre-built integrations with your current systems.
Examples of Inventory Management Software
Small businesses can choose from various software options depending on their needs and scale. For example, a small retail store might use a simple cloud-based solution, while a larger wholesale business might require a more comprehensive enterprise resource planning (ERP) system.
Implementing an Automated Inventory System
Implementing an automated system requires careful planning and execution. A phased approach minimizes disruption and ensures a smooth transition.
Step-by-Step Implementation Process
- Needs assessment and software selection
- Data migration from existing systems
- System setup and configuration
- Staff training and onboarding
- Go-live and initial monitoring
- Ongoing optimization and refinement
Implementation Checklist
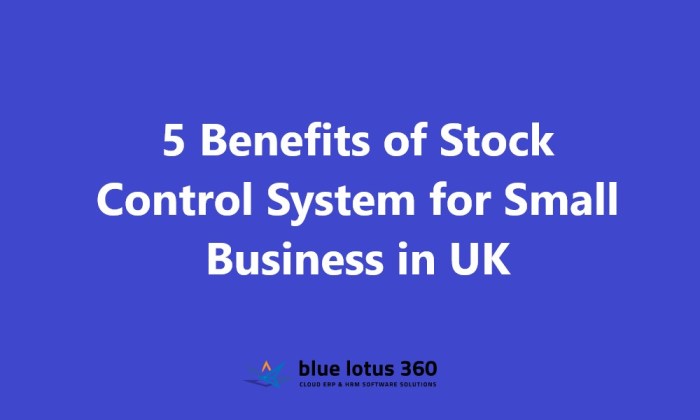
Source: bluelotus360.com
- Software purchase and installation
- Data cleanup and preparation
- Barcode/RFID label printing
- Staff training materials development
- Testing and quality assurance
- Post-implementation support plan
Staff Training Requirements
Comprehensive training is crucial for successful adoption. Training should cover all aspects of the new system, including data entry, reporting, and troubleshooting. Hands-on training and ongoing support are essential.
Best Practices for Data Migration
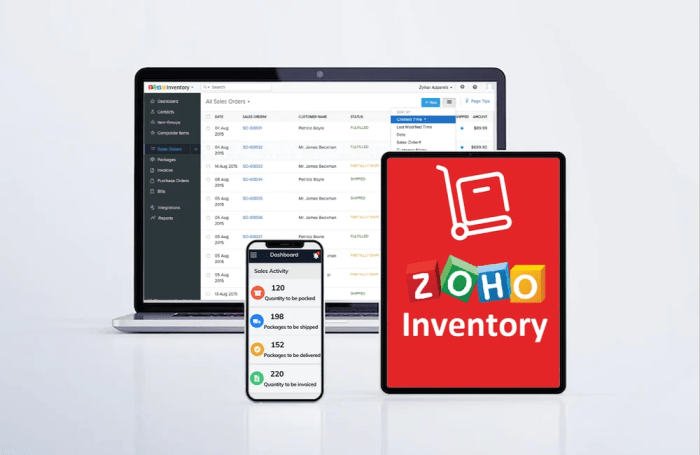
Source: imimg.com
Data migration should be carefully planned and executed to ensure data accuracy and integrity. Data cleansing, validation, and reconciliation are essential steps. Consider using a phased approach to minimize disruption.
Optimizing Inventory Control Processes
Optimizing inventory levels minimizes waste and storage costs. Automated systems enable better demand forecasting and efficient order management.
Strategies for Optimizing Inventory Levels
Implement strategies like Just-in-Time (JIT) inventory, Economic Order Quantity (EOQ) calculations, and safety stock management to balance supply and demand. Regularly review and adjust inventory levels based on sales data and market trends.
Using Automated Systems for Demand Forecasting
Automated systems leverage historical sales data and other factors to predict future demand. This allows for proactive ordering, reducing stockouts and minimizing excess inventory.
Importance of Regular Inventory Audits
Regular inventory audits and reconciliation are essential to ensure accuracy and identify discrepancies. Automated systems can simplify this process by comparing physical counts with system records.
Automated Inventory Control Workflow
- Order placement (through automated system or integration)
- Supplier notification and order processing
- Goods receipt and inventory update (barcode/RFID scanning)
- Storage and management of inventory
- Order fulfillment and shipment
- Inventory level monitoring and adjustments
Analyzing and Improving Inventory Performance
Monitoring key performance indicators (KPIs) is crucial for evaluating the effectiveness of the automated system and identifying areas for improvement.
Key Performance Indicators (KPIs)
Track KPIs such as inventory turnover rate, carrying costs, stockout rate, fill rate, and order fulfillment time. Analyze trends and identify areas needing attention.
Tracking and Analyzing Inventory Turnover Rates
The inventory turnover rate indicates how efficiently inventory is being sold. A high turnover rate generally suggests efficient inventory management, while a low rate may indicate overstocking or slow-moving items.
Improving Inventory Accuracy and Reducing Stockouts
Regular inventory audits, accurate data entry, and efficient order management processes contribute to improved inventory accuracy and reduced stockouts.
Reports from Automated Inventory Systems
Automated systems generate various reports, including inventory valuation reports, sales analysis reports, low-stock alerts, and performance dashboards. These reports provide valuable insights into inventory performance and help identify areas for improvement.
Security and Data Management: Automate Inventory Control Small Business
Protecting inventory data is crucial. Robust security measures and data backup procedures are essential.
Importance of Data Security and Backup Procedures
Implement strong password policies, access controls, and regular data backups to protect against data loss or unauthorized access. Consider cloud-based solutions with built-in security features.
Ensuring Data Accuracy and Integrity, Automate inventory control small business
Regular data validation, reconciliation, and audits ensure data accuracy. Implement processes to detect and correct errors promptly.
Compliance with Data Privacy Regulations
Adhere to relevant data privacy regulations, such as GDPR or CCPA, when handling customer and inventory data. Ensure compliance through appropriate data security measures and policies.
Automating inventory control for small businesses offers significant efficiency gains. Streamlining this process is easier than you might think; consider leveraging technology like dedicated mobile apps. A great resource to explore is this helpful guide on android apps for small business inventory , which can significantly improve your inventory management. Ultimately, choosing the right tools for automation will save you time and money in the long run.
Addressing Potential Data Breaches or System Failures
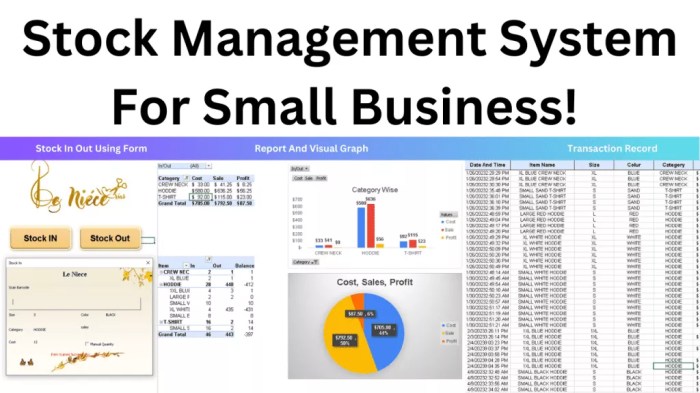
Source: msexcelvba.com
Develop a comprehensive incident response plan to address potential data breaches or system failures. This plan should include procedures for data recovery, notification of affected parties, and remediation.
FAQ Overview
What are the common hidden costs associated with implementing inventory management software?
Hidden costs can include data migration expenses, employee training time, potential integration complexities with existing systems, and ongoing subscription fees.
How do I choose the right inventory management software for my specific industry?
Consider industry-specific features. For example, a restaurant might need features for perishables, while a retailer might prioritize features for managing multiple locations.
What if my employees are resistant to adopting new inventory software?
Thorough training, clear communication of the benefits, and addressing concerns proactively are key to successful adoption. Highlighting time savings and reduced workload can be persuasive.
How often should I conduct inventory audits after implementing an automated system?
While automation reduces manual counts, regular audits (monthly or quarterly) are still recommended to ensure data accuracy and identify any discrepancies.